Hazard:
A VSC employee recently suffered life threatening injuries while installing a new sprinkler system beneath a conveyor. His arm became pinched and rolled into a large conveyor belt causing major trauma.
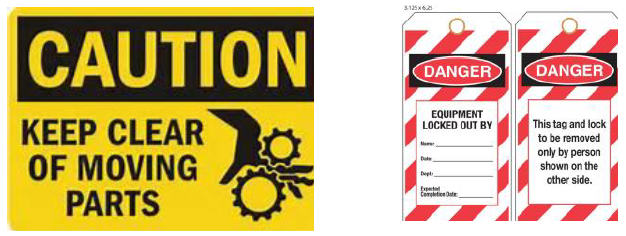
VSC performs services, maintenance and construction work near equipment with moving mechanical systems. The potential hazards from these exposures are pinching, caught-in-between, electrocution, struck-by & crushing bodily injuries. VSC’s Lockout-Tagout Safety Policy was created to address these hazards.

A number of VSC customers are manufacturing, industrial, and shipping industries with the type of machinery & mechanical processes seen here:
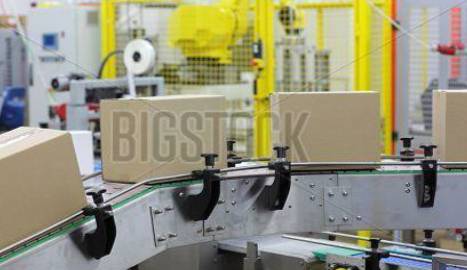
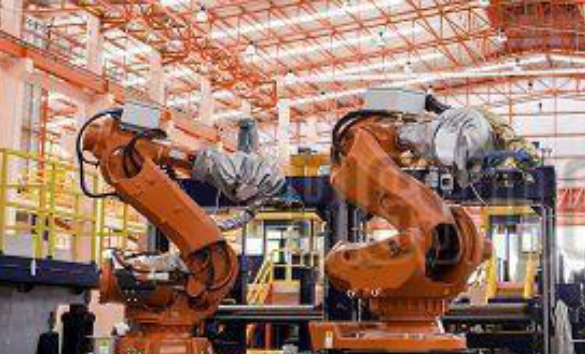
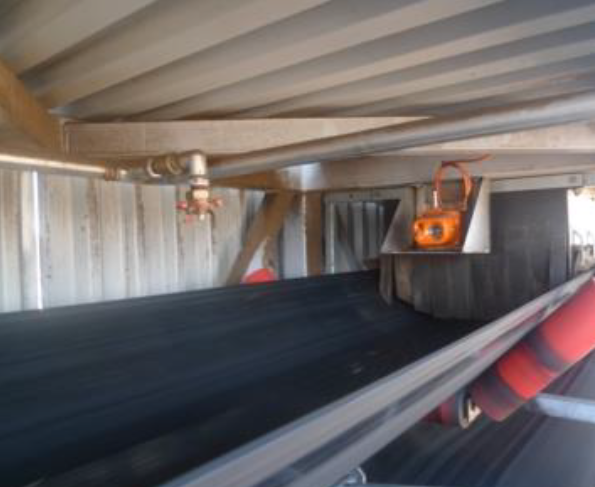
VSC installs sprinkler and alarm systems in close proximity and often inside, above & beneath this hazardous equipment. The potential for injury is very high. Even when accessing your work area you may have to come in close contact with machinery.
Gears, chains, rotating pulleys & belts can grab and pull in fingers, arms & legs resulting in severe injuries.
Preventative Measures:
- Federal and state safety laws known as LOCK OUT TAG OUT (LOTO) require deactivation of controls for this equipment and render them inoperative prior to starting work. This safety standard is mandatory even if work is not actually performed on the equipment. When there is a potential for direct or indirect contact with these hazards LOTO must be implemented.
- To help reduce hazards the VSC district office responsible for the project must coordinate VSC’s work with customer site management personnel. This may require shutting down the customer’s production operations.Communication and coordination with the customer is required! VSC’s Risk Management can assist in these discussions. Maintenance technicians representing the customer are usually the most knowledgeable resource in identifying the controls specific to the equipment. The supervisor must establish contact with maintenance to ensure operational processes are secured and safe for us to perform work. This procedure may require VSC technicians to complete the customers LOTO safety training.
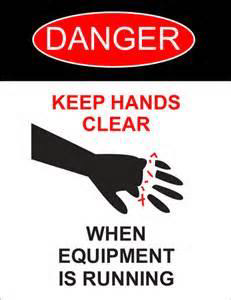
In addition to a customer’s safety procedure for locking out and deenergizing equipment, VSC must include our own lockout tag out program to ensure equipment is inoperative. The VSC supervisor will perform a site walk through with each technician who will be performing the work. Each technician will be assigned an individual tag and lock that he will install himself. VSC’s Lockout-Tagout Safety Policy describes this process in detail, but the following is a basic guide:
There are three basic steps when implementing LOTO.
- Deenergized
- Rendered Inoperable
- Verify equipment shut down
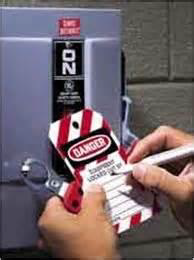
Step 1
The switch or breaker is shut off and tagged & signed by person attaching
the tag.
Step 2
A lock or other device is attached to prevent reactivation. This is performed by the same person who signed the tag.
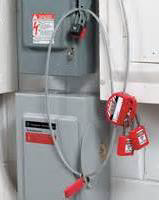
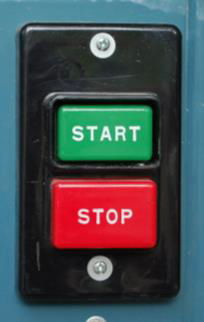
Step 3
Locate and test the correct start button or switch to verify equipment will not
activate.
Step 3 Alternate
Equipment with control levers to activate mechanical parts must also be tested to verify machinery is inoperable.
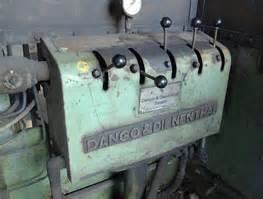
The final step is to verify all equipment is inoperable and there are no other controls that can reactivate the equipment. This procedure must also be performed by the same person implementing steps 1 & 2
VSC Fire & Security Risk Management can be contacted for any assistance with these LOTO procedures.