WEEK 1
HORESPLAY- ZERO TOLERANCE
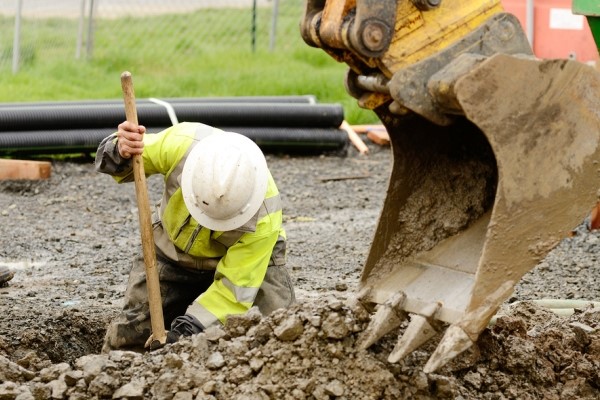
An operator of an excavator struck a water line while digging a trench, causing water to spray around. A worker in the trench took his shovel and started tossing water back at the excavator operator.
The operator was trying to close the window against the water when he inadvertently hit the lever controlling the bucket. The bucket moved, crushing the other worker against the wall of the trench.
Horseplay starts in fun, but can easily end in tragedy. In this case, the water line break was enough of a distraction to cause a safety concern without the added confusion of a water fight. Don’t give in to the temptation of workplace pranks; they take everyone’s mind off the number one priority of working safely.
WEEK 2
LUCKY ESCAPES
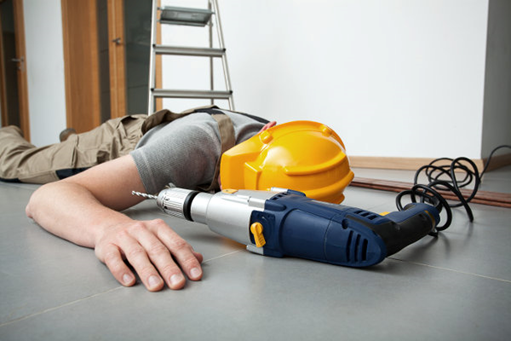
Close call incidents do not often result in injuries.
However, ignoring a close call means you could be paving the way for a serious injury to happen. You must report all close calls so they can be investigated and the hazard removed before someone does get hurt. For every reported first aid or minor injury, there are on average hundreds of close calls incidents that have gone unreported.
Close calls (also known as near misses) are situations in which a worker has a narrow escape from getting hurt. The worker probably feels lucky about getting away uninjured. If we pay attention, these incidents can be lucky in another way: They provide a preview of an injury that could happen, so measures can be taken now to prevent it.
Here’s an example: A carpenter’s assistant picks up a power drill and gets a slight electric shock. He quickly drops the tool, suffering no injury. At this point, he has an important choice to make. If he just forgets the incident, the next person to pick up the tool may have damp hands or may be standing in a puddle of water. That person is bound to get a severe shock. However, if the incident is reported, the tool will be removed from service, checked over and either repaired by qualified personnel or discarded. There will also be a chance to find out why this tool became defective. Was it poorly designed or manufactured? Has the insulation been allowed to get wet or is the cord frayed? How can problems be avoided in the future – perhaps by buying better tools, taking good care of them and inspecting them regularly?
WEEK 3
Anger: Just One Letter Short Of DANGER
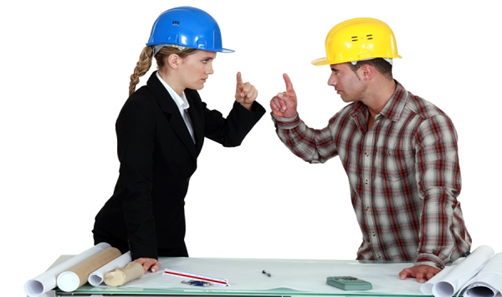
If you have angry workers in your department or you yourself are angry, you may end up reporting more injuries on the job. A recent study by the Annals of Family Medicine found that high levels of anger increase the risk of injury. Angry people are more likely to sustain injuries serious enough to require emergency medical care, and the risk is higher for men than women, says lead author Daniel Vinson of the University of Missouri. The study found that nearly 32% of all the patients reported being irritable just before they were injured, 18% reported being angry and 13% reported being hostile. Anger more than quadrupled a person’s odds of being injured, while being hostile increased those odds sixfold. For men, Vinson says, the link was particularly clear. Another study that followed 100 drivers for two weeks linked episodes of anger with “near accidents”. Two additional studies found that angry people were more likely to have car crashes or sustain football injuries. There is little doubt that anger can be a contributing factor in workplace injuries, but what do you do about it? Here are some tips:
- Consciously determine to be calm. Don’t react, think! Remember your goals and respond appropriately. Communicate. When someone upsets you, tell them. Calmly talk to them about how you feel about their words or actions. Learn to express yourself better — clear and composed.
- Remove yourself. Get away from the scene until you can respond without anger. Your success will not happen overnight. Take it one step at a time, one day at a time. Remember to relax. Relaxation exercises or music can be helpful. Keep in mind you can reach out to someone you trust for help.
- Frequently take time for yourself. Do something you enjoy like walking in the park, swimming, reading the Bible, or seeing a feel-good movie. Do something nice for someone you admire. It’s okay to feel good about yourself. Look for the positives. Don’t dwell on the negatives. “Don’t sweat the small stuff.” Don’t worry about things that are out of your personal control. This is difficult, but an attitude and behavior that can be learned
WEEK 4
Who Is Responsible For Safety?
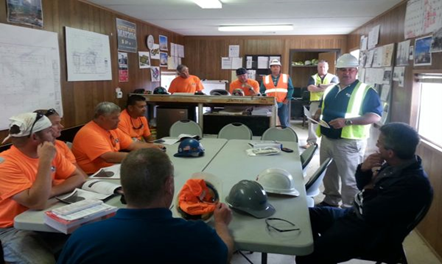
Safety is everyone’s responsibility! As an employee, you should:
- Learn to work safely and take all rules seriously and recognize hazards and avoid them.
- Report all accidents, injuries and illness to your supervisor immediately.
- Inspect tools before use to avoid injury.
- Wear all assigned personal protective equipment.
On the other hand, it is management’s responsibility to:
- Provide a safe and healthy workplace and provide personal protective equipment.
- Train employees in safe procedures and in how to identify hazards.
Everyone must be aware of potential hazards on the job:
- Poor housekeeping results in slips, trips and falls.
- Poor material handling may cause back problems or other injuries.
- Tools and equipment can cause injuries if guards or protective devices are disengaged.
Always use the protections that are provided on the job:
- Machine Guards keep body parts from contacting moving equipment.
- Personal protective equipment shields your body from hazards on the job.
In case of emergency:
- Know how to notify emergency response personnel.
Safety benefits everyone. With fewer injuries, a business can be more productive and profitable. By incorporating safety rules, employees avoid injury as well as illness from exposure to hazardous substances.
“SAFETY IS PRIORITY NUMBER 1!”