FALL PROTECTION INSPECTION OF EQUIPMENT
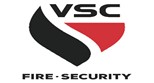
Pre-Use Inspection-Prior to use, each worker must inspect the fall arrest equipment they will use for defects or damage. Also remember to follow the manufactures instructions for proper tag inspection, VSC also requires to you to follow the five year rule of the manufactures date provided on the tag.
Harness Inspection:
a. Labels
All labels must be present and fully legible so you can see the manufacture date, type of harness expected weight limits
b. Stitching
If any stitches are pulled or broken, the harness must be removed from service. Closely inspect “critical stitching” which will be in a color that contrasts with the webbing.
c. Webbing
Inspect for cuts, tears, stretching of fibers, fraying, raveling of edges, excessive wear or abrasion, chemical damage, burns, UV degradation, and weld splatter. Hold hands six to eight inches apart and flex webbing into a “U” shape to reveal frayed or broken fiber. The presence of hardened or discolored spots on the webbing indicates chemical or excessive heat exposure.
d. Connectors
Inspect all metal components including “O-rings”, “D-Rings” leg grommets, chest strap connecting hardware, and adjustment components. Look for cracks, heat damage, distortion, corrosion, and excessive wear.
e. Cleaning and Storage Instruction
Excessive accumulation of dirt, paint, or other foreign matter may prevent proper function of the harness, and in severe cases, weaken the webbing. Store the harness in a dry place, out of direct sunlight, preferably hanging by the rear D-ring.
Lanyard Inspection:
a. Labels
All labels must be present and fully legible with the last annual inspection less than 12 months prior to the current date documented on the inspection tag.
b. Connectors/Snap hooks
Make sure connectors are operating properly. Snap hook must have a double locking mechanism that does not allow latch to open without releasing the first lock, and springs into locked position when released. Also inspect for cracks, distortion, or corrosion.
c. Shock Absorber
Inspect all areas of the cover. The cover should not be torn or damaged. Ensure the webbing content of the absorber has not been stretched, or Un-stitched in anyway. Remove from service if defective
What is the hierarchy of controls?
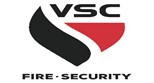
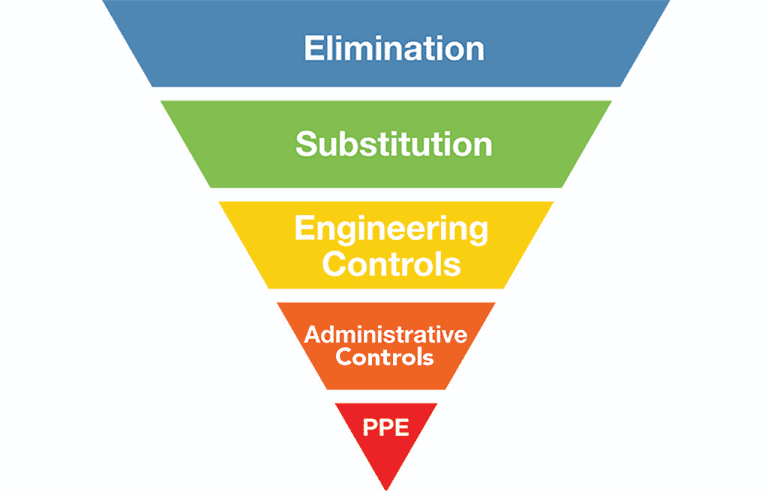
The hierarchy of controls is a system used in the construction industry to minimize or eliminate exposure to hazards. The hierarchy of controls has five levels of actions to reduce or remove these hazards, sorted from most to least effective:
- Elimination
- Substitution
- Engineering Controls
- Administrative Controls
- Personal Protective Equipment
Elimination– The best solution in any hazardous situation would be to physically remove the hazard. “Elimination” is the preferred solution to protect workers because without the hazard present, no exposure or injury can occur.
Substitution– The next best solution would be to use substitution, or replace the hazardous object, material, or process with something less hazardous. Before working in a hazardous situation, evaluate if there is an option that isn’t as hazardous. This could involve actions such as using a safer tool to get the job done or swapping out a toxic substance for an environmentally-safe material.
Engineering Controls– Aim to isolate workers from the hazard. When performing a hazardous task, evaluate if there are any engineering controls that you can implement to keep the employee safer. This includes things such as physical barriers, equipment guards, and ventilation systems.
Administrative Controls–Are put in place to change the way people work. These include things such as job training, job rotation, breaks, company policies, etc. Administrative controls limit exposure to hazards by adjusting work tasks or schedules. For example, not all employees may need to be on a jobsite when a hazardous task is being performed, limiting the number of employees at risk.
PPE– Is used as a last resort to protect the worker from the hazard. The task you are performing will determine how much or how little PPE you should wear to protect yourself. Some examples of PPE are:
- Gloves
- Steel Toe Shoes
- Respirator
- Safety Glasses/Face Shields
- Earplugs
- Hard Hats
Recognized Versus Unrecognized Hazards
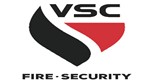
Being able to recognize hazards in the workplace is very important. There are so many different hazardous situations that can be present in many workplaces. It is important to have training about these substances. That way you are able to spot out harmful situations.
Working at a company for several years doesn’t put you at any less risk for hazardous conditions. New employees are sometimes more aware than experienced ones. That is because it is so easy to become complacent in your job. Which one do you think is more dangerous: hazards that you are able to recognize, or ones that go unrecognized?
The Dangers of Unrecognized Hazards-Are you trained to recognize jobsite hazards? That is an important part of beginning a job that different situations can be harmful. Letting things happen and go unrecognized can result in injuries or fatalities. It is very important for the safety of yourself and your fellow employees to have the proper training to be responsible on the job.
It is a common occurrence that when someone has been working the same job for many years, they get complacent. That isn’t always on purpose, it can happen without you even realizing it. For the safety of everyone working, it is vital that you stay aware of the hazards that can occur. No matter how long an employee has been on the job, all hazards should be addressed.
Electrocution- A lot of times construction zones are in an area with electrical wires—either below ground or above—creating a hazard of being electrocuted and injured. Electrocution has been the reason for many work related deaths. It is important to take the time to recognize where all electrical wires are located. Then, take the correct electrical safety measures to be as safe as possible when working around them. Each employee would benefit from basic knowledge of working with electricity.
Heavy Equipment and Moving Vehicles- There are normally a lot of different tasks going on all at once on a construction site. That includes moving vehicles and pieces of heavy equipment. When workers are able to walk near moving equipment, it can result in struck-by incidents. This can be avoided by having zoned areas. That way you can minimize the occurrence of someone not being noticed and getting hit. There are also hazards of these pieces of equipment tipping or rolling. If safety precautions are in place to help protect them can make these situations safer.
Collapsing Structures-There are many different scenarios for construction work. Not only are you building structures, but you are also tearing them down. There are instances that someone could be in the wrong place at the wrong time with results being a structure collapsing on them. Site inspections should be done, and schedules should be stuck to.
The Dangers Of Working Alongside Subcontractors
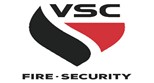
Anytime that you add in a new task to a job, there is the potential for hazards. The workers present in the area that new tasks are being added to are most at risk. They have created a routine for the job that they do, now they are needing to rearrange everything. The dangers that are present when working with other companies are there for both sides. Subcontractors are in a new environment and don’t know how everything flows on the worksite. Anytime someone is in a new environment, it takes time to learn the ropes.
Ways To Work Around Subcontractors
Working around subcontractors may be a difficult task to maneuver. It is a necessary one though. Jobs have to be completed and without this process, they wouldn’t get done. It is important to find a good way to work around each other and both sides get their jobs done. Here are some helpful tips on ways to do that.
Meet Prior To Starting
Each day on a construction site can be different. Tasks get completed and need to keep moving on to the next step. Meet with the subcontractors at the beginning of each day, that way you can arrange a good schedule. One that is safe for all crew members who are working.
Speak Up
If you are working and notice something not done correctly, don’t hesitate to take it to a supervisor. When a subcontractor’s employee isn’t following protocol, make it known. This is going to help the worksite be safe and avoid unnecessary injuries.
Communication Will Help
If there is no communication between you and the subcontracting crew, it will be hard to execute the job. Let them know how your crew works and what is expected. Make them aware of the hazards that can come up and what to do when it does. Talk to them about the safety precautions that are in place. Safety precautions are going to vary depending on the work getting done. The subcontractors can’t follow them if they are not made aware of them.
Stop Work For Hazards
When a hazard has been brought to attention, all work needs to stop. This way the issue can be safely taken care of. You always want to avoid injuries to crew members at all costs. Talk to the subcontractor and see how they normally work. Figure out what their expectations are and how they execute their jobs. This way you can work together and make a plan to work for both people. There are many other items to take into consideration and please discuss with the sub contractors when they arise, think about this while you are working in the field.